Chlorine-containing potentially corrosive aftermarket engine oil treatments
ISSUES:
The use of aftermarket engine oil supplements that contain
chlorine can cause corrosive wear to a vehicle’s engine
and possible subsequent engine failure.
TECHNICAL DISCUSSION:
Aftermarket engine oil supplements are “treatments” advertised
to enhance an oil’s properties. Manufacturers
claim these treatments reduce friction, noise and wear;
maintain higher lubricity and break down sludge and varnish,
protecting the engine components. Many products
advertise materials like Tefl on, molybdenum or graphite;
however, most fail to mention that they contain chlorine,
which can be highly corrosive when mixed with water.
Chlorinated paraffi ns were once used as extreme pressure
(EP) additives in lubricants, but the practice has been
discontinued in most passenger vehicle lubricants due to
the corrosive side effects. These chlorinated compounds
are used due to their low cost and ability to provide EP
properties, but they readily react with water and combustion
by-products to form acidic materials that promote corrosion
of engine components and bearings.
Lubes ‘N’ Greases published an article in August 1998
outlining the effects of chlorine on vehicle engine components.
Author Maurice LePera explains the following:
Chlorinated additives are not used in modern, fully
formulated automotive engine oils. The environment
within an internal combustion engine consists of high
operating temperatures, combustion and blowby
gases, moisture, acid and oxidation precursors, wear
debris, unburnt fuel, etc. The combination of these
ingredients when combined with the catalytic effects
of metallic surfaces and trace soluble metals such as copper will cause chlorine to hydrolyze – forming
hydrochloric acid and other associated reaction products.
Once generated, these acidic reaction products
can cause serious internal engine corrosion problems,
especially on ferrous and aluminum alloys.1
Furthermore, chlorinated paraffins tend to become more
reactive as temperatures rise, making them exponentially
more dangerous in hotter environments.
“Chlorine-based additives can be film-forming even at
ambient temperatures, but as the temperature rises they
become aggressive and, with the release of HCl [hydrochloric
acid], can cause signifi cant corrosion.”2
Corrosion on the cam lobe or tappet face can also cause
corrosive spalling, outlined in an engine failure case later
in this bulletin.
Because of the side effects of chlorine breakdown, many
military and commercial specifications prohibit the use of
chlorinated additives. For example, military specification
MIL-PRF-17331J specifies, “[additives], if used, shall not
contain chlorine.”3 Furthermore, “SAE J357 (Physical and
Chemical Properties of Engine Oils) lists chlorine as a
contaminant.”1
AMSOIL INC. recently initiated an independent lab study
to determine if four engine treatment products contained
chlorinated ingredients, and if so, how much each contained.
The products tested were Dura Lube Engine
Treatment Booster, Motorkote Hyper Lubricant/Engine
Treatment, Motorkote MK Million Mile Formula and Prolong
Engine Treatment. Dura Lube4 and Prolong6 make no
reference to chlorine content in their product descriptions;
Motorkote5 makes no reference in some of their product
descriptions, while others specifi cally state “contains no
chlorine.” However, based on the lab testing, each contains
high amounts of chlorine as referenced in the following
table.
Engine Treatment Product |
Chlorine, ppm (%) |
Dura Lube Engine
Treatment Booster |
55,000 (5.5) |
Motorkote Hyper Lubricant
/Engine Treatment |
272,000 (27.2) |
Motorkote MK Million
Mile Formula |
207,000 (20.7) |
Prolong Engine Treatment |
304,000 (30.4) |
Each oil additive contained signifi cant quantities of chlorine
as tested by ASTM D-808. Typical lubricating fl uids
contain anywhere from 0 to 150 ppm of chlorine, which is
considered a trace amount.
A recent AMSOIL Technical Services investigation on a
Cummins OTR ISX-485 engine failure revealed a high
amount of chlorine in the engine oil.
The Cummins parts analysis determined the engine failure
was the result of a corrosive attack to the cam follower
pins, causing valve and injector camshaft lobe failures
(see Figures 1-2). Five injector lobes and four valve lobes
were significantly spalled, meaning the metal flaked off
the surface of the lobes. Analysis of the injector pin and
valve pin showed corrosive attack in both the wear and
non-wear areas of the pins, while severe galling was observed
on the cams and cam follower pins. Galling is the
transference of material when moving parts are no longer
fully separated and protected. Furthermore, surface analysis
showed peaks of chlorine in the actual metal surface,
which is not normally present on a cam follower pin under
normal operating conditions (see Figure 3).
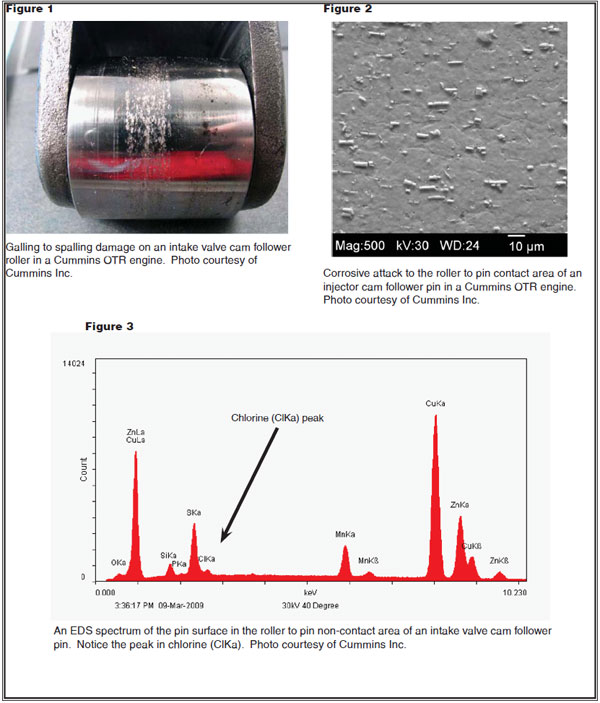
The chemical data on the lubricant and surface analysis of
the failed engine parts revealed the root cause of the failure
was corrosive wear. Acidic components in lubricants
directly lead to corrosive wear. In this case, an abnormal
amount of chlorine was found in the engine oil. Chlorine,
when combined with hydrogen and water in the engine,
can create hydrochloric acid. This, in turn, can cause severe
TBN depletion, which was the case with this Cummins
engine. It was determined that a chlorine-containing additive
was used when an oil sample from the engine tested
at 11,000 ppm of chlorine. The result was an extreme corrosive
environment which was responsible for the upper
end engine failure within 195,000 original miles.
RECOMMENDATION:
Aftermarket oil additives are not recommended for use
with AMSOIL synthetic motor oils. AMSOIL synthetic motor
oils are fully formulated to provide superior protection
and performance; use of aftermarket additives will detract
from their performance and possibly lead to engine failure.
Use of aftermarket oil additives not approved by AMSOIL
INC. will void the AMSOIL Limited Warranty.
REFERENCES:
1. LePera, Maurice. (1998, August). Chlorine & Engine
Oils: A Good Mix? Lubes ‘N’ Greases, pp. 16-20.
2. Rudnick, Leslie R. (2003). Lubricant Additives Chemistry
and Applications. New York, New York: Marcel Dekker,
Inc.
3. MIL-PRF-17331J. (2003, September 09). Retrieved from
http://www.wbdg.org/ccb/FEDMIL/prf17331j.pdf.
4. Dura Lube Products. (2008). Retrieved from https://www.duralube.com/Galleries/Small/DL%20booster%20sell%20sheet.pdf.
5. Motorkote Products. (2008). Retrieved from https://www.motorkote.com/Products.aspx.
6. Prolong Super Lubricants. (2010). Retrieved from http://www.prolong.com/A_ET.html.